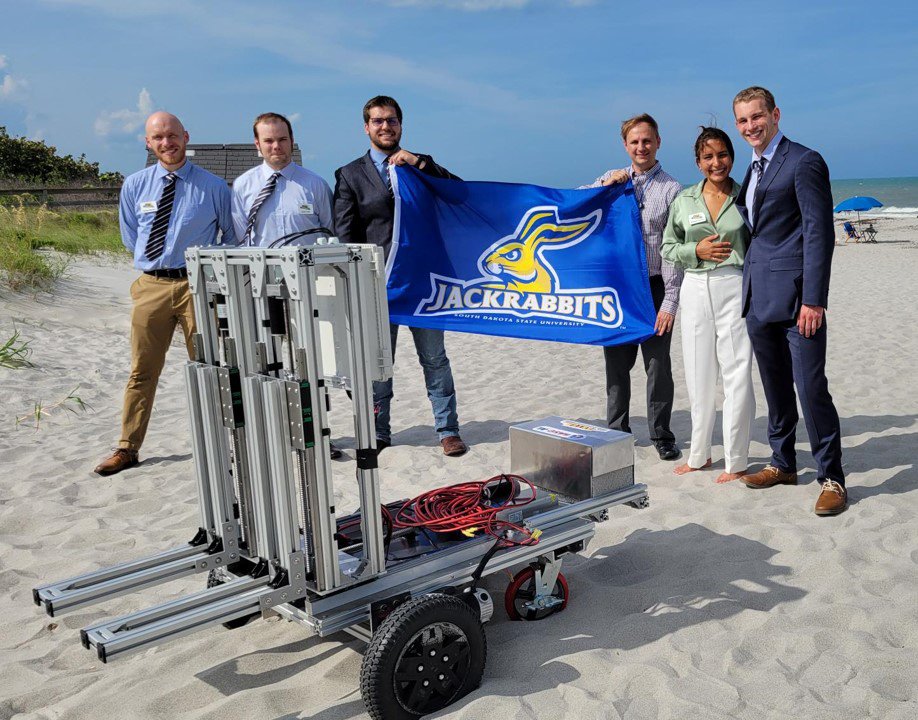
South Dakota State University engineering students used down-to-earth knowledge to design an out-of-this-world lunar transport vehicle which won them a NASA-sponsored contest.
The SDSU team was one of 15 teams selected as a finalist in NASA’S Revolutionary Aerospace Systems Concepts – Academic Linkage (RASC-AL) competition. Finalists were grouped in four categories. SDSU was one of four universities chosen as finalists in the Lunar Surface Transporter Vehicle category along with Maryland, Texas and Virginia Tech.
All 15 finalists gathered in Cocoa Beach, Florida, June 12-14 to present their projects to NASA judges. The space agency released contest results June 15.
In addition to having the best plan for a lunar transport vehicle, SDSU was honored for building the best prototype of any of the 15 finalists.
NASA also awarded a top overall winner and runner-up. Both of those awardees came from the Homesteading Mars category. Projects from Massachusetts Institute of Technology and the University of Puerto Rico – Mayaguez, respectively, were chosen to present their work at a space conference in Las Vegas Oct. 23-25.
Todd Letcher, an associate professor in the mechanical engineering department and the adviser for the SDSU students, said of his team, “I’ve probably never had a team that worked together so well. They had their assigned areas, but when someone needed help, they all pitched in and got the job done. They are also very good writers. The papers turned out well. They’re very competitive people. They all wanted to win.”
Team members were Liam Murray, Omaha, Nebraska; Jacob Pettit, Dublin, Ohio; Ben Sobczak, Rapid City; Nick Stegmeier, Sioux Falls; and Elisabeth Timmer, Savaneta, Aruba; all graduated May 6 with degrees in mechanical engineering and are now heading off for full-time jobs, master’s degrees or in the case of Stegmeier, an internship at Johnson Space Center in Houston.
The power of an ANT
The name of the SDSU project is Artemis Navigating Transporter System, and the theory behind their project draws heavily on its acronym—ANTS.
Murray said, “The initial thought was having multiple robots connect together and form one big robot. We soon realized that would add too many variables. We discussed having several smaller rovers (eventually ANTS) that have many more advantages and functions when it comes to being innovative while accomplishing the competition guidelines.”
What the students ended up with was a highly customized forklift.
In their executive statement, the students wrote, “Our lunar cargo transporter features an innovative drivetrain, flexible wheels, a cargo locking mechanism and a universal attachment mechanism for auxiliary systems. The vehicle is adaptable not only for missions on the moon, but for Mars and beyond.”
Using rounded numbers, the design for each forklift is 11 feet by 11 feet and 9 feet high with an ability to lift 16,500 pounds.
Full-scale model size of VW Bug
Stegmeier explained, “The prototype is about the size of a go-cart while a full-scale ANT would be as large as a Volkswagen Bug, which is quite fitting. Two key features of the ANTS system are the collaborative lift capability, allowing the ANTS to lift very large and heavy payloads such as astronaut habitats, and the use of linear actuators and screws to enable the lifting systems, rather than the typical hydraulic systems that Earth-based forklifts use.
“Hydraulic systems are difficult to use on the lunar surface due the vacuum of space, making it difficult to keep a seal; and the likelihood of lunar dust contaminating the hydraulic system. We didn’t have time to build two ANT prototypes, which would enable demonstration of the collaborative lifting, so we decided to demonstrate the feasibility of a screw-driven lifting system.
“The ANT demonstration prototype has two screw-driven forks that can be controlled individually or synchronously. This enables lifting cargo on uneven terrain. For stability during cargo transport, the entire forklift assembly can be translated over the center of the prototype chassis using another screw and actuator.
Letcher looks forward to next year
“In addition, our prototype can be remotely controlled, just like the real ANTS system.”
While the students have gone their separate ways, the prototype is being shipped back to campus and Letcher has plans to display it in the lobby of the Chicoine Architecture, Mathematics and Engineering Hall with the two plaques the team received.
Letcher already is looking forward to fielding a team for next year’s contest. “This was such a good experience,” he said.
- Contact:
- Telephone number: 605-688-4538
Republishing
You may republish SDSU News Center articles for free, online or in print. Questions? Contact us at sdsu.news@sdstate.edu or 605-688-6161.